Differences and benefits of single and double flanged track wheels
As surprising as it may sound, the first wheels ever invented were used outside of transportation. Discovered in 3500 B.C. in Mesopotamia, the first wheels in civilization served as potter’s wheels. It wasn’t until 300 years later that wheels would be used for transportation as chariot wheels. The wheelbarrow then appeared in classical Greece, between the 6th and 4th centuries B.C., and eventually made its way into China and medieval Europe.
The pivotal role of wheels in transportation has grown exponentially throughout history and continues today, from large-scale public transportation to industrial and commercial operations. There are unique benefits to flanged rail wheels—both single and double flanged—and specific applications that fully make use of their defining characteristics.
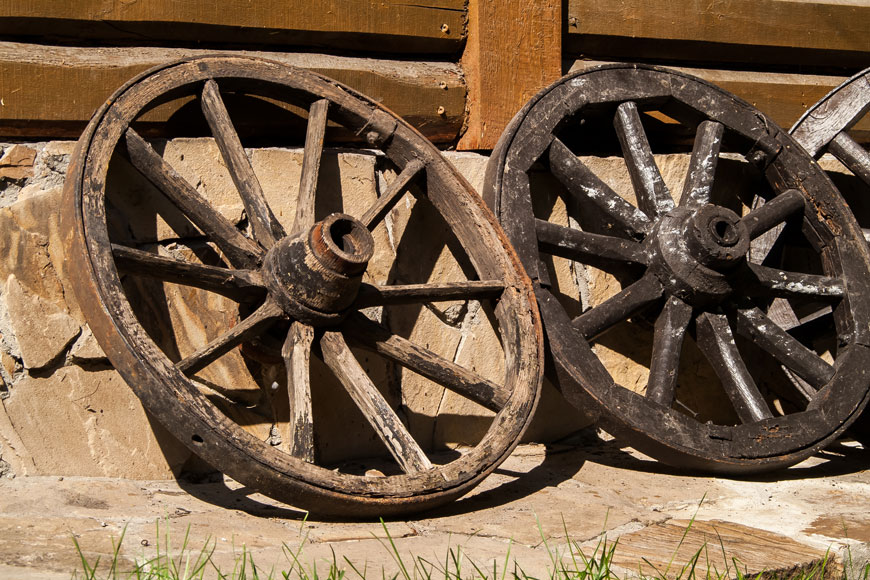
Flanged rail wheels
A flange refers to the projecting edge or rim on the circumference of a steel wheel that is designed to keep the wheel on a rail. Rail transportation with flanged wheels is ideal when carrying loads between fixed locations on a regular basis. Loads can include people, raw materials, or products. Metal tracks offer low-friction movement, high-capacity loading, and exceptional durability. They are also self-guiding, and do not need to be steered by a driver.
Flanged wheel rail installations rely on a different type of precision and design than the wheels on a car or shopping cart. Rubber or plastic tires are made from softer materials to create traction with flat surfaces. Contrastingly, metal wheels used on tracks use precise geometry and engineering to keep them on course.
How flanged wheels work
One might think the flange—the additional rim or lip that protrudes beyond the tread of the wheel—is what keeps a vehicle on track. However, this isn’t the case for most conventional rail applications.
Wheels are manufactured with a tapered tread—making them slightly cone-shaped—and installed on a fixed axle causing each wheel to rotate at the same rate. Their cone shape allows one wheel to spin with a faster tread speed than the other. This is important when going around a bend, where the inside rail is shorter than the outside. To keep both wheels spinning at the same rate—and to keep the train on its tracks—the wheelset shifts to one side. The wider portion of the wheel tread travels the greater outside distance, and the smaller portion of the opposite wheel travels the shorter inside distance.
Why flanged wheels are necessary
If a flange isn’t required to keep a wheel on track, why have it? Although a wheel can be designed to stay on track without a flange, it is crucial as a safety feature.
For a train or trolley travelling a curve too fast—or where rails may be bent or untrue—a flange helps to ensure vehicles stay on track. In fact, the high-pitched squealing that can be heard when a train goes by is often caused by the flange rubbing against the rail. Wheels are meant to roll with as little friction as possible, and contact with wheel flanges introduces undesirable metal-on-metal rubbing.
Single flanged wheels
Single flanged wheels refer to a wheel with a flange on only one side of its tread. They are commonly used for most trains and trollies, as well as other commercial and industrial vehicles with fixed axles running on trued rails. Wheels are fixed to their axle in most rail applications, so a single flange on each wheel is enough to prevent movement in either direction.

Double flanged wheels
When is a second flange necessary?
- Operating conditions are not as controlled
- Safety is of special concern
Many material transfer vehicles don’t have the benefit of operating in clean, controlled conditions. Lumber drying kilns are a prime example. Kiln operators typically transport lumber in and out of kilns using metal rail configurations. Due to the extreme weight requirements and high-impact loading, rail conditions are often less than ideal. It’s not uncommon to see rails warped at varying angles from each other, making conventional track applications impossible.
Even when tracks are in poor condition, rail installations still offer high-capacity, low-friction transportation. For warped rails, wheels can be installed with bearings so that they rotate at their own speeds. They can also be designed to drift across a portion of an axle to accommodate bent rails. Due to the wheels moving independently of each other, these wheels require a flange on either side of the tread to ensure they stay on track.
Double flanged wheels are also common for overhead cranes, where truck assemblies may span significant distances, and safety is a key concern. Rather than rely on a fixed axle or crossbeam to align single flanged wheelsets, double flanges help ensure that each wheel tracks independently for more secure movement.
Most wheels that depend on double flanges to stay on track feature a flat tread, as the tapered geometries typical of single flanged wheels don’t offer any benefit—in this case, it is the flanges that keep the wheels on track.
Material selection for metal wheels
Several factors determine what type of wheel is most suitable for a particular application. It’s also important to consider material design characteristics. Double flanged wheels, for example, will see frequent contact between the flange and the rail, making wear and strength an issue in the long term. Although wheel flanges are not necessarily designed to withstand significant loads or impact, wheel strength is still an important factor to consider.
Cast iron vs. steel flanged wheels
An important distinction to make is the difference between cast iron, ductile iron, and steel wheels. Cast iron is typically cheaper to manufacture, but it is a much harder and more brittle material. Not only will it wear the track quicker, but it is more susceptible to fracture. Ductile iron is also a widely used material for wheels as it provides some measure of the cost savings that cast iron wheels exhibit over steel, but it exhibits physical properties closer to those of steel rather than cast iron. Steel is a more robust metal, with the strength and ductility that is often needed for industrial applications—especially where excessive contact with the flange is expected.
Other factors to consider include:
- Load capacities
- Operating speeds
- Environmental conditions

The material, size, and shape of a wheel will all affect load capacity. Although casting can be used to manufacture wheels, it does present a lot of waste in production. Wheels can often be produced more effectively and efficiently as forgings, or as machined parts from stock steel—such as rounds, shafts, plates, and bars.
Environmental conditions, such as heat and exposure to chemicals, can also affect design. A range of steel alloys are available to suit different conditions to avoid corrosion and potential failure.
Choosing the right wheels
Understanding the mechanism and function of wheels, and knowing what your project’s wheel requirements are is key to avoiding broken parts and work stoppages—saving money in the long run. Both single and double flanged wheels offer unique benefits for track applications. Making the right wheel choice will not only increase efficiency, but, more importantly, ensure the ongoing safety of equipment and workers involved in operation.

References:
Smithsonian – http://www.smithsonianmag.com/science-nature/a-salute-to-the-wheel-31805121/